Discovering the Fundamentals of Welding Examination: An In-depth Assessment of Procedures, Tools, and the Significance of Quality Assurance in Welding Industries
Welding examination offers as a keystone in the maintenance of safety and structural integrity across various sectors. Recognizing the implications of these techniques raises essential concerns about their effectiveness and the future direction of high quality assurance in welding.
Relevance of Welding Evaluation
Welding assessment plays a crucial role in guaranteeing the stability and safety of bonded frameworks. It acts as a methodical technique to evaluating weld high quality, recognizing possible issues, and making certain compliance with established requirements and specs. The relevance of welding examination extends beyond simple adherence to regulations; it is crucial in protecting human lives and protecting investments in facilities.
Faulty welds can cause disastrous failings, leading to substantial financial losses, injury, or loss of life. Strenuous assessment procedures are vital to spot issues such as insufficient infiltration, porosity, or fractures before they rise right into critical failings. In addition, reliable welding assessment contributes to the general performance and longevity of frameworks, making sure that they can hold up against the conditions for which they were designed.
Moreover, the implementation of welding evaluation cultivates a society of top quality and accountability within the welding market. By focusing on inspection, companies demonstrate their commitment to quality, thereby enhancing their credibility and competition in the market. Ultimately, welding evaluation is not just a procedural step but a basic part of engineering stability and safety assurance, crucial for the successful implementation of welding projects throughout various sectors.
Key Evaluation Processes
An extensive strategy to welding inspection entails several essential procedures that are important for ensuring weld quality and architectural honesty. The first crucial process is aesthetic assessment, which enables inspectors to recognize surface area flaws such as splits, porosity, and incorrect grain appearance. This approach functions as a preliminary examination to make sure that the weld meets specified standards.
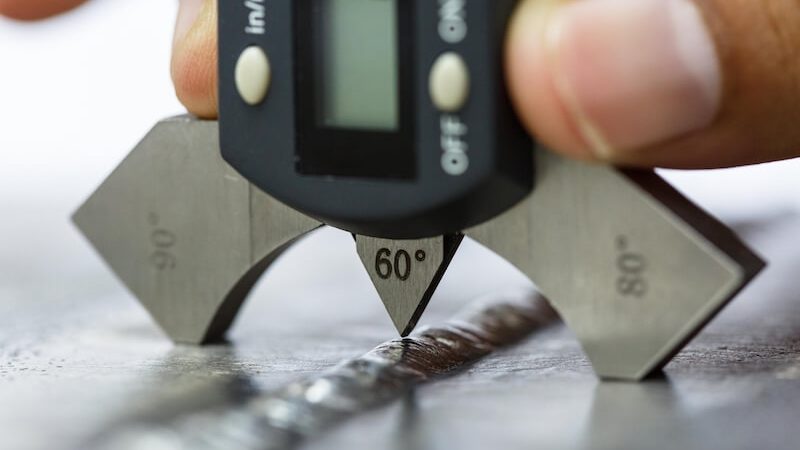
Furthermore, harmful testing might be performed on example welds to assess their mechanical residential or commercial properties and performance under tension. This process entails impact, tensile, and exhaustion testing to verify that the weld can stand up to operational conditions.
Last but not least, documents and coverage are critical components of the examination process. Maintaining exact records of inspections, monitorings, and examination results helps ensure compliance with industry standards and helps with constant improvement in welding practices. Jointly, these key procedures form the foundation of efficient welding examination and quality control.
Devices for Weld Examination
Numerous tools are vital for effective weld examination, each developed to analyze various facets of weld high quality and performance. Among the most commonly utilized are aesthetic inspection devices, including magnifying glasses and borescopes, which allow inspectors to determine surface area problems such as fractures, porosity, and inappropriate blend.
Additionally, ultrasonic testing (UT) equipment is critical for discovering interior defects. This device uses high-frequency sound waves to disclose interruptions within the weld, making certain the honesty of the material. Radiographic testing (RT) devices, which utilize X-rays or gamma rays, likewise supply understanding into the inner structure of welds, enabling the identification of incorporations or voids.
For specific measurements, calipers and gauges play a considerable duty in identifying weld measurements and ensuring adherence to specified resistances. Solidity testers review the mechanical residential or commercial properties of the weld, guaranteeing it satisfies performance criteria.
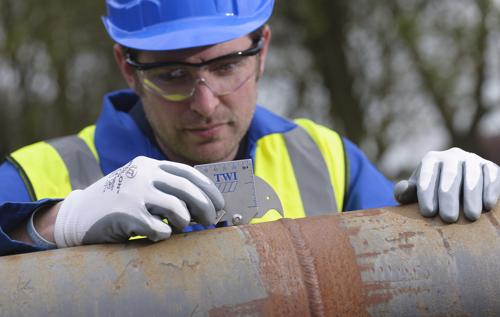
Techniques for Analyzing Quality
How can the high quality of welds be his comment is here reliably assessed? A selection of methods are used to assess weld stability and make sure adherence to specified requirements.
Ultrasonic screening (UT) is an additional noticeable strategy that makes use of high-frequency acoustic waves to discover inner flaws within the weld. Houston Welding Inspection. This approach supplies a thorough sight of the weld's stability without compromising its architectural stability. On top of that, radiographic testing (RT) uses X-rays or gamma rays to expose interior problems, using detailed understandings into weld high quality
Magnetic bit screening (MT) works for identifying surface area and near-surface stoppages in ferromagnetic products, making use of electromagnetic fields and tinted fragments to highlight flaws. Lastly, color penetrant screening (PT) can be employed to reveal surface-breaking defects by using a dye that seeps right into fractures and is subsequently disclosed.
Conformity With Sector Specifications
Conformity with market standards is essential for ensuring the high quality and safety and security of bonded frameworks. These criteria, established by companies such as the American Welding Culture (AWS) and the American National Requirement Institute (ANSI), give standards that control the welding process, products, and evaluation methods. Sticking to these requirements not just makes sure the structural stability of welds but likewise alleviates dangers related to failings that could bring about catastrophic effects.

Welding assessors are tasked with validating conformity with these requirements throughout the welding procedure (Houston Welding Inspection). This involves analyzing welding procedures, monitoring welder qualifications, and carrying out extensive examinations of the final item. Non-compliance can lead to considerable economic repercussions, project hold-ups, and damages to a company's online reputation
Furthermore, conformity promotes a society of top quality control within the company. By developing clear assumptions Learn More and criteria, business can keep consistency in their result and boost overall productivity. Regular training and updates on criteria are important to keep personnel educated and experienced, making sure that all facets of welding procedures satisfy or surpass regulative requirements. Eventually, commitment to sector standards functions as a foundation for excellence in the welding sector, advertising safety and integrity in bonded structures.

Verdict
In conclusion, welding evaluation offers as an important component in maintaining the security and integrity of welded structures. Adherence to market standards guarantees compliance and promotes a society of top quality within the welding industry.
In addition, the implementation of welding inspection cultivates a culture of high quality and liability within the welding sector. Inevitably, welding evaluation is not simply a procedural step but an essential element of design honesty and security guarantee, essential for the effective implementation of welding tasks across various industries.
A comprehensive method to welding examination entails a number of crucial processes that are necessary for ensuring weld high quality and architectural honesty. These standards, established by organizations such as the American Welding Culture (AWS) and the American National Standards Institute (ANSI), provide guidelines that govern the welding procedure, materials, and evaluation methods.Welding examiners are entrusted with verifying conformity with these standards throughout the welding procedure.